Don't Get Duct Up! Your Guide to Crawl Space Ductwork
Understanding Your Crawl Space Ductwork
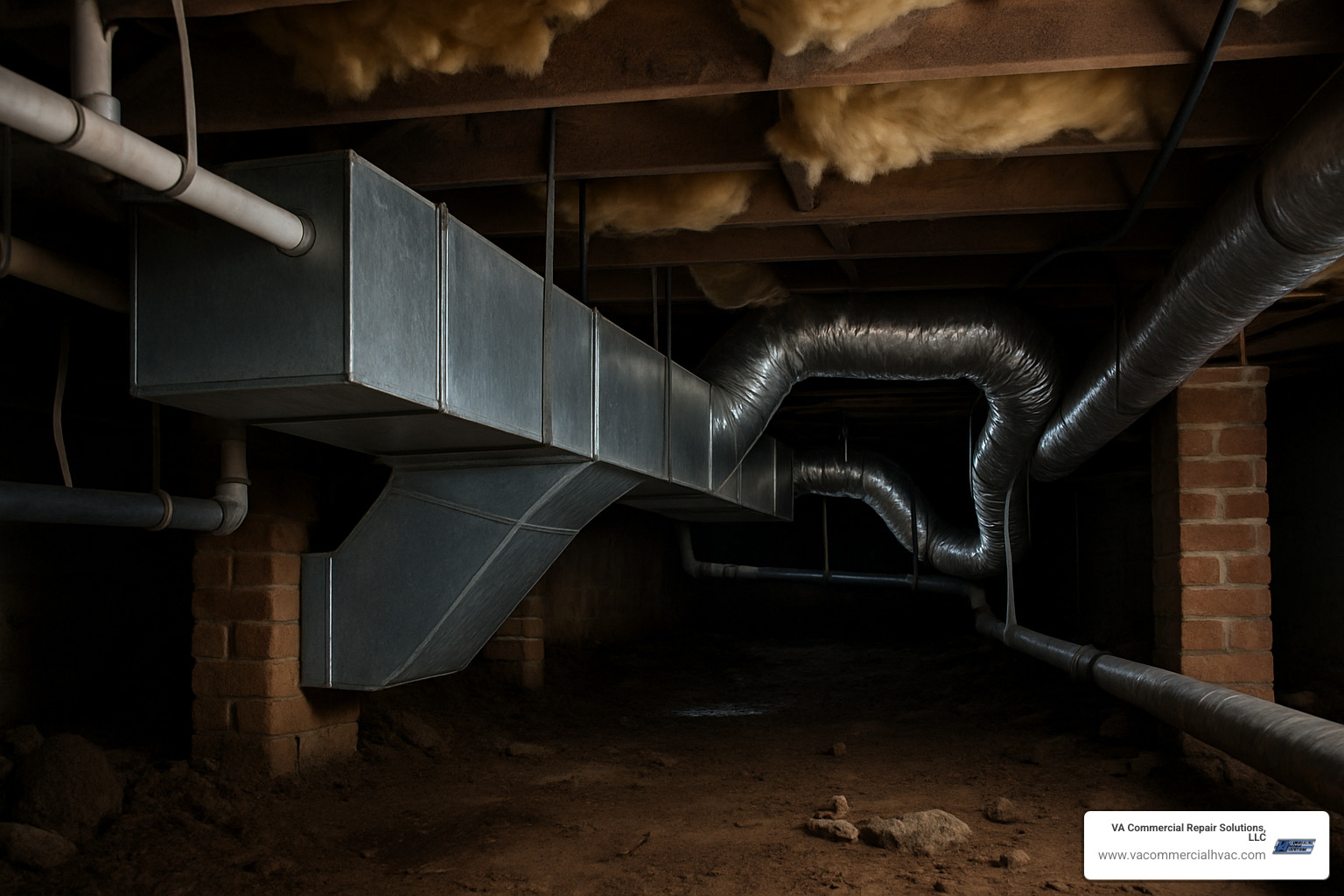
When you search for crawl space ductwork , you usually want two things fast: what it is and why you should care. In most Central Virginia buildings, the ducts that feed your HVAC system run through a shallow, unconditioned area beneath the floor. Builders often choose this route because it’s a cost-effective and straightforward way to keep plumbing, wiring, and HVAC lines consolidated in a single service corridor without sacrificing interior space.
However, this convenience comes with a significant trade-off that directly impacts your building's health and your bottom line:
- Massive Energy Loss : Uninsulated or poorly sealed ducts in a crawl space are exposed to outdoor temperature swings. In a hot Virginia summer, your cool, conditioned air is running through a super-heated environment. In winter, the opposite occurs. The result is that your HVAC system has to work much harder to maintain the desired indoor temperature. The U.S. Department of Energy estimates that leaky ducts can dump 20-30% of your heating and cooling into thin air before it ever reaches your vents.
- Severe Air-Quality Hits : Your HVAC system circulates all the air in your building multiple times per day. If the ducts have gaps, cracks, or loose connections, they create negative pressure that sucks in the surrounding crawl space air. This air can be contaminated with moisture, mold spores, dust mites, pest droppings, and even dangerous soil gases like radon. This contaminated air is then distributed directly into your workspace, contributing to musty odors, allergies, and sick building syndrome.
- Costly Moisture Damage : The combination of cold metal ductwork and a humid crawl space is a perfect recipe for condensation. As warm, moist air hits the cold duct surface, water forms—a phenomenon known as “sweating.” This constant moisture drips onto insulation, wooden floor joists, and subflooring, leading to wood rot, mildew, and a perfect breeding ground for mold and pests like termites.
If persistent musty odors, unexplained spikes in utility bills, or inconsistent temperatures are plaguing your business, your crawl space is the first and most important place to investigate. This guide will walk you through why ducts are located there, the specific problems that arise, and the most effective fixes to ensure your business retains its comfort—and its cash.
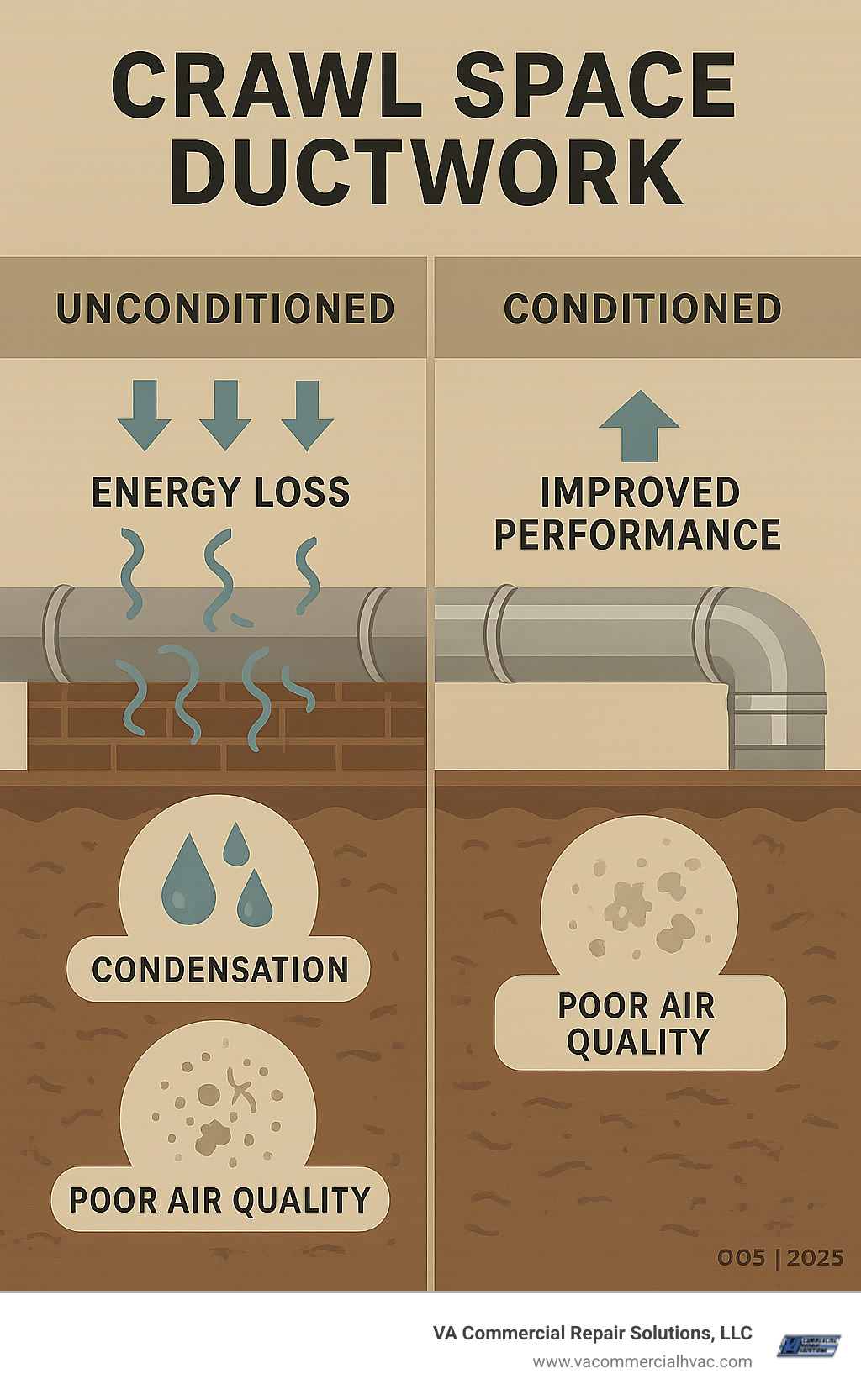
Understanding Crawl Space Ductwork
Think of your HVAC system as the circulatory network for your building. The supply trunk is the main artery, delivering conditioned air from the air handler to individual rooms. The return trunk is the main vein, bringing stale air back to be reheated or recooled. In Virginia, these critical arteries and veins often run through the crawl space because it's a less expensive construction method than building dedicated interior chases or soffits.
Materials matter significantly in this harsh environment. Flexible duct , or "flex duct," is a tube made of a spring-steel wire helix, covered by a plastic liner, a layer of fiberglass insulation, and an outer vapor barrier. It's popular because it's cheap and easy to snake around obstacles. However, it's also prone to tearing, kinking, and sagging if not properly supported, all of which restrict airflow and create leaks. Sheet-metal duct is more durable, offers less resistance to airflow, and lasts much longer. But it's more expensive and labor-intensive to install, requiring each joint and seam to be carefully sealed.
Regardless of the material, once ductwork is placed outside the thermal boundary of the building (the insulated shell separating conditioned from unconditioned space), it is forced to fight outdoor temperatures year-round. Why do builders and property owners stick with this setup? The primary drivers are affordability, easy access for future repairs, and established building code allowances. In Virginia, codes typically require a minimum of R-8 insulation on these ducts. The key to making this system work is to aggressively mitigate the inherent downsides before they drain your operational budget and compromise your indoor environment.
Conditioned vs. Unconditioned Crawl Spaces
In a typical unconditioned (or vented) crawl space, your 55°F supply air might travel through 90°F, high-humidity air in the summer, or 40°F air in the winter. This extreme temperature difference forces your HVAC system into overdrive and creates a prime environment for condensation. For decades, building codes mandated vents in crawl spaces with the belief that they would help dry out moisture. However, modern building science has proven this to be incorrect, especially in humid climates like Virginia's. In the summer, these vents do the opposite: they pull in warm, moisture-laden air that condenses on cooler surfaces, leading to the very problems they were meant to prevent. Research consistently shows that total HVAC system energy loss can be as high as 25% when ducts are located in vented crawl spaces.
Factor | Conditioned | Unconditioned |
---|---|---|
Energy loss | 5-10 % | 15-25 % |
Avg. humidity | < 50 % RH | > 60 % RH |
Mold risk | Low | High |
Conditioning or encapsulating a crawl space transforms it into a clean, dry, semi-conditioned area. This process involves sealing off the vents, laying a heavy-duty vapor barrier over the ground, insulating the foundation walls instead of the floor above, and then conditioning the air with a small supply vent and/or a dehumidifier. According to ENERGY STAR , this approach brings the crawl space temperature and humidity much closer to the levels inside the building, typically within 10-15°F of indoor levels. This dramatically reduces energy loss from the ductwork and eliminates condensation issues. While there is an upfront investment, many encapsulation projects pay for themselves in just 3-7 years through significant reductions in utility costs and the avoidance of expensive repairs for mold and rot.
Common Crawl Space Ductwork Problems & Diagnostics
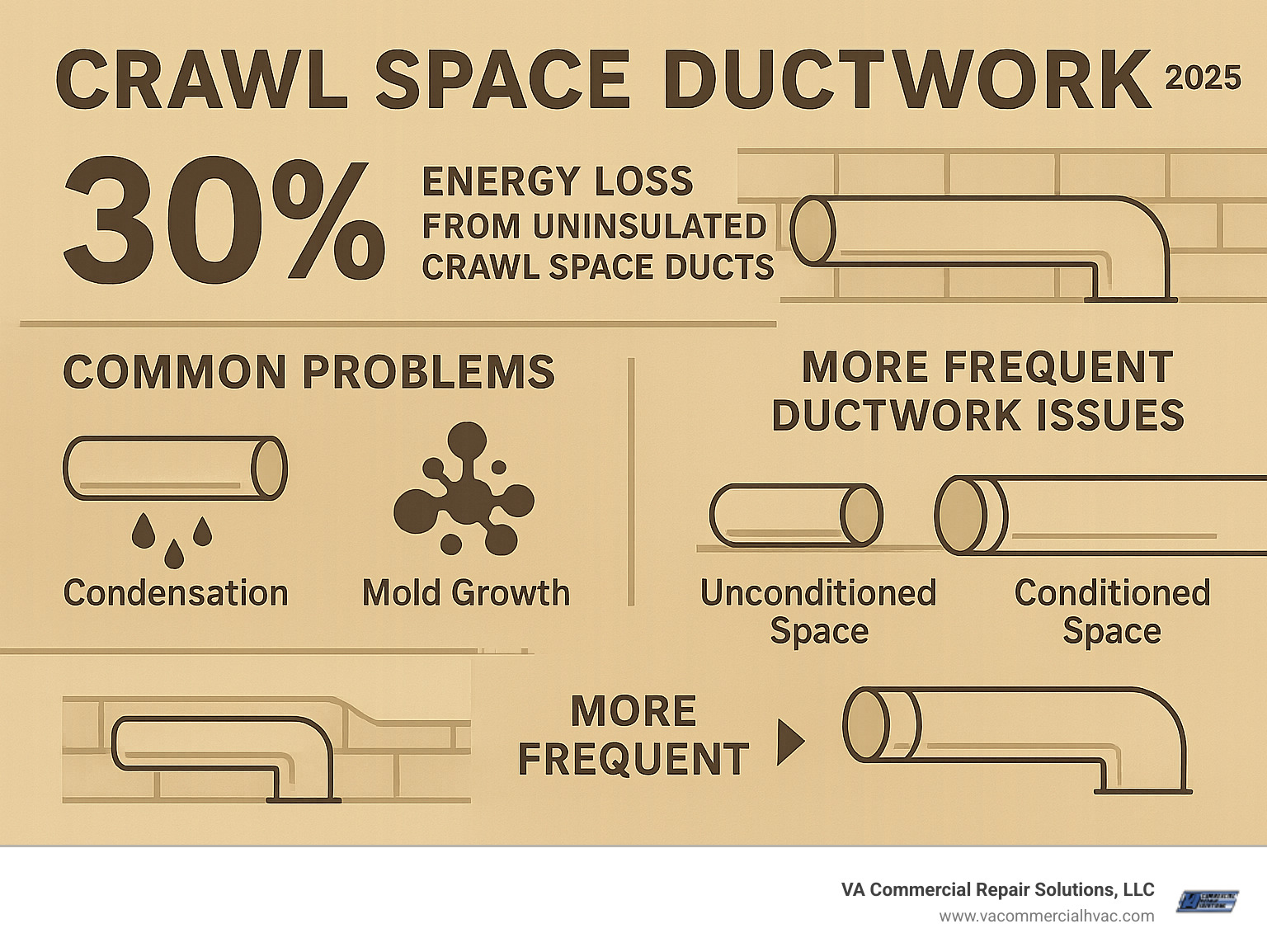
Your crawl space ductwork is under constant assault from moisture, pests, and temperature extremes. These are the top troublemakers we find in Central Virginia businesses:
- Condensation : This is the most visible and destructive issue. When your AC runs in the summer, the duct surface temperature can drop to 55°F. When the warm, humid crawl space air (often at 80-90% relative humidity) hits this cold surface, it cools below its dew point, and the water vapor condenses into liquid. This “sweating” soaks insulation, making it useless, and drips onto wood, fueling mold growth and structural rot.
- Air Leaks : Leaks occur at every connection point: where ducts meet the main plenum, at wye-junctions, and especially where the duct boot connects to the floor register. Even small gaps can have a huge impact, wasting up to 20% of your system's output and, more importantly, actively pulling dirty crawl-space air into your breathing air supply.
- Damaged or Missing Insulation : Rodents and other pests love to tear apart fiberglass insulation for nesting material. Over time, the wrap can also sag, get crushed, or fall off entirely. A compressed or wet piece of insulation loses nearly all its R-value, leaving the duct completely exposed to the crawl space environment.
- Corrosion : The high humidity in an unconditioned crawl space is tough on sheet metal. Over years, moisture can cause galvanized steel ducts to rust, especially at the seams and joints. This corrosion eventually leads to pinholes and cracks, creating a network of tiny leaks that are hard to spot but collectively cause major energy loss.
- Pressure Imbalances : Large leaks, especially on the return side of the system, can depressurize the entire building. This negative pressure can cause dangerous back-drafting of combustion appliances like furnaces and water heaters, pulling carbon monoxide into your property. It also increases the infiltration of soil gases like radon.
Key warning signs include musty odors, unexplained hot or cold spots, steadily rising utility bills, visible moisture or frost on ducts, or rattling sounds from loose connections. To diagnose these issues, professionals use tools like smoke pencils to visually identify leaks, thermal imaging cameras to spot insulation gaps, and a duct-blaster test to pressurize the entire system and precisely measure total air leakage in CFM (cubic feet per minute).
Best Practices for Sealing, Insulating & Upgrading
Fixing crawl space ducts isn't just about patching a hole; it's about creating a durable, long-lasting system. The professional standard follows a clear order of operations for maximum effectiveness.
- Seal First : The most critical step is to make the ducts airtight. This is best done with a thick, paint-on mastic sealant. Mastic is applied generously over every joint, seam, and connection, creating a flexible, permanent seal that won't crack or peel over time. For larger gaps (over 1/8 inch), fiberglass mesh tape is embedded in the mastic for reinforcement. While UL-181 foil tape is a valid option for small, clean applications, it often fails in the dirty, humid conditions of a crawl space. Tape alone never lasts.
- Insulate Next : Once the seals are cured, the ducts must be properly insulated. The code-minimum is typically R-8 foil-faced wrap . It's crucial that the insulation is wrapped snugly but not compressed, as crushing it reduces its R-value. The foil facing acts as a vapor barrier, preventing moisture from reaching the duct surface. Mineral-wool sleeves are another excellent, moisture-resistant option.
- Support Every 4 Feet : Flexible ductwork must be supported by wide nylon or metal straps at least every 4 feet to prevent sagging. Dips and kinks in the duct line create airflow restrictions and places for moisture and dust to collect.
- Foam the Boots : A major source of leakage is the gap between the metal duct boot and the wooden sub-floor. This gap should be sealed from below using spray foam to create a permanent, airtight connection.
Quick DIY Air-Sealing Checklist
For minor, accessible issues, a motivated owner can perform basic sealing:
- Gently remove any loose or contaminated insulation. Wear gloves, goggles, and a respirator (N95 or better).
- Thoroughly clean all metal surfaces at joints and seams with a rag and denatured alcohol to remove dust and oils.
- Using a disposable paintbrush, slather a thick layer of mastic over all seams and connections. If you can see a gap wider than 1/8 inch, apply fiberglass mesh tape over it and then cover with mastic.
- Allow the mastic to cure for at least 24 hours, or as directed by the manufacturer.
- Re-wrap the connection with foil-faced insulation. Keep it fluffy, not crushed. Secure the insulation with wire ties or straps every 18-24 inches.
- Use UL-181 foil tape to seal all the seams on the outer insulation wrap itself.
If your crawl space has persistent high humidity (above 60%), standing water, or a history of flooding, duct repairs alone are a temporary fix. Full crawl-space encapsulation is the comprehensive solution that addresses the root cause by removing the source of moisture, protecting your ducts and the entire building structure.
Cost, Installation & Maintenance Roadmap
Investing in your ductwork is an investment in energy efficiency and air quality. Here are some ballpark costs you can expect for professional service in the Central Virginia area. These can vary based on crawl space accessibility, material choices, and the extent of the damage.
- Flex Duct Replacement : $30 - $40 per linear foot
- Sheet-Metal Replacement : $40 - $60 per linear foot
- Typical Full System Swap (in an average-sized commercial space) : $2,600 - $7,300
- Minor Repairs (Seal & Re-insulate specific sections) : $450 - $2,400
A good rule of thumb: if more than 20-25% of your duct system is tangled, torn, or damaged, a full replacement is often more cost-effective in the long run than piecemeal repairs. Extremely tight, low, or difficult-to-access crawl spaces can add a 5-15% labor premium to the total cost.
Maintenance for Longevity
Proper maintenance can significantly extend the life of your ductwork and prevent major failures.
- Quarterly : Change your HVAC system's air filters. Clogged filters increase pressure in the duct system, which can strain seams and connections over time.
- Annually : Perform a visual inspection of the crawl space. Look for any sagging ducts, torn insulation, signs of pest activity, or visible moisture on the ductwork. Ensure support straps are still secure.
- Every 3-5 Years : Consider a professional inspection. A technician can check for subtle signs of trouble, touch up any failing mastic or tape seals, and perform a pressure test if you suspect performance has declined.
While simple tasks like changing filters and visual inspections are manageable, major work like replacing trunk lines, redesigning the system for better airflow, or performing a certified duct-blaster test should always be handled by a licensed HVAC crew. This ensures code compliance, protects your equipment warranty, and guarantees the work is done safely and effectively.
Frequently Asked Questions about Crawl Space Ductwork
How do I know if my ducts need replacement instead of just repair?
Persistent moldy smells that don't disappear after cleaning, visible rust pinholes or widespread corrosion on metal ducts, or energy bills that remain high after basic sealing are strong indicators of systemic failure. If the duct system is over 15-20 years old and a professional inspection reveals that more than one-fifth of the ductwork is damaged, kinked, or contaminated, replacement is almost always the better long-term investment.
What R-value is required for crawl space duct insulation?
Most Virginia jurisdictions and modern building codes call for a minimum of R-8 insulation on any ducts located in unconditioned or vented areas. However, R-value is only effective if the insulation is installed correctly. It must be kept dry and fluffy. Insulation that is compressed, wet, or has gaps no longer meets its rated R-value and is non-compliant.
Can I seal the ducts myself?
You can certainly tackle small, easily accessible, and visible joints with mastic and foil tape, provided you use the proper safety gear (gloves, mask, eye protection). However, you should always leave major work to a professional. This includes any situation involving potential asbestos-containing materials (common in buildings from the 1980s or earlier), widespread mold contamination, or any work that requires redesigning or recalculating duct sizes for proper airflow.
Can I use regular gray "duct tape" to seal my ducts?
Absolutely not. Despite the name, standard cloth duct tape should never be used to seal HVAC ducts. The adhesive is not designed to withstand the temperature fluctuations and humidity found in a duct system. It will quickly dry out, become brittle, and peel off, leaving the leak worse than before. Always use proper UL-181-rated foil tape or, preferably, mastic sealant.
What's the difference between duct sealing and crawl space encapsulation?
Duct sealing specifically targets the HVAC ductwork itself, patching leaks and insulating the ducts to reduce energy loss. Crawl space encapsulation is a whole-building solution that treats the entire crawl space. It involves sealing off outside vents, laying down a vapor barrier, and insulating the foundation walls to turn the crawl space into a clean, dry, semi-conditioned area. Sealing your ducts is good; encapsulating the crawl space is better because it eliminates the root cause of moisture and temperature problems.
Will sealing my ducts really lower my energy bills?
Yes, significantly. According to ENERGY STAR, sealing and insulating ducts can improve the efficiency of your heating and cooling system by as much as 20 percent — and sometimes much more. When you stop paying to heat and cool your crawl space, that savings goes directly to your bottom line. The exact amount depends on the severity of the leaks, but it's one of the most effective energy-saving upgrades you can make.
Conclusion
Properly sealed and insulated crawl space ductwork is not a luxury; it's a fundamental component of an efficient, healthy, and comfortable commercial building. Taking action can cut your utility waste by up to 30%, deliver cleaner air to your employees and customers, and reduce the strain on your expensive HVAC equipment, extending its lifespan. Don't let your profits and comfort leak through the floor.
For businesses in Charlottesville, Harrisonburg, Waynesboro, Staunton, Lexington, Fishersville, and the surrounding counties, VA Commercial Repair Solutions is ready to help. We keep businesses running 24/7 with a commitment that sets us apart: no voicemail, just live help from a real person, day or night. Our repair-first service philosophy means we focus on finding the most cost-effective solution, and we back our work with solid guarantees.
Ready to stop losing money through the floor? Our expert team is on call for immediate inspection, professional sealing, or complete crawl-space solutions. Call us anytime for a fast response and a permanent fix.